Casting Other Metals
I know some of you will be wondering about bronze. I haven’t tried it yet. I am told you can do it with the same sort of furnace, but you’ll probably want a real clay crucible and smaller charcoal. You need to burn fuel a lot faster for higher temperatures. There are also some tricky things with getting the right flux cover on the metal to avoid gas bubbles. Worse, you can’t cook it very long or you boil off the tin before the copper can fully melt. Then you have to add more tin and you have no idea what alloy you’re working with. Maybe someday I’ll be willing to bother.
Another possibility is iron. You need a lot of heat, but no worries about alloys. I haven’t found any need to do this yet, but I know a group of guys who make cast iron art, and I went to one of their melts. Here’s a brief tour of their operation.
They have fancy molds made from soft refractory blocks that are exotic compared to my sand from the building supply store. (My sand would probably be melted by molten iron and fuse to the casting.)

Some are open-faced molds made with a Dremel directly in the refractory.
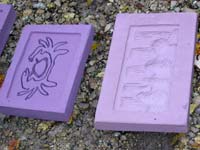
One fellow had a vertical mold.
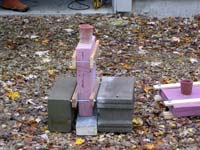
And this is a huge, complicated mold.

Here you can see a ladles preheating with a gas burner driven by an old vacuum cleaner fan. They have two ladles the size of my entire furnace!

The buckets all contain coke, iron or flux. A cupola furnace can go through a lot of materials in a hurry.

Here’s the cupola preheating. Notice the protective gear? If you think molten aluminum is hot…

Here one of the guys is putting in the bod plug – a little clay chunk that stops up the furnace while it starts melting.

After adding the fuel and metal, it was not long before the gas burners were replaced with blowers. I was amazed how quickly thereafter the furnace could be tapped. I’m pretty sure it was faster than my little furnace melts a crucible of aluminum. (On the other hand, one of the artists was passing out the products of his home distillation experiments, so I don’t trust my sense of time completely.)

While these guys started pouring, two more guys were filling the next ladle.
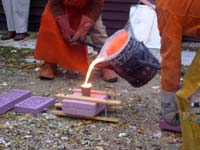
For that really big mold they needed two, so they tapped one and kept it hot with a piece of refractory insulation over the top. Then they started pouring when the second ladle was almost full. These guys have lots of experience.

Here’s the gang posing after the pour.
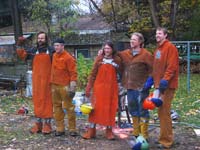
Now the real work starts, chipping hardened refractory out of the rough castings.

Here’s one closer to cleaned off.

And of course the big arch that took two ladles of iron.
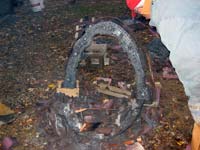
That was a wonderful afternoon, but as cool as all this looks, I think aluminum will keep boaty types busy for more time time than most of us want to spend off the water.
Dangers
As you might imagine, some cautions are in order. As I mentioned last month, molten aluminum is 10 times hotter than boiling water. It can mess you up in a hurry. If you spill it on anything wet there will be an explosion from water instantaneously bursting into superheated steam. This can make concrete explode and of course throws molten metal everywhere. This is bad. Do your homework on safety if you’re going to attempt this, and think through every step carefully. I know I’m harping on this, but it’s important.
Or do like Chuck does and send the patterns to a foundry.
But the real danger with this isn’t the hot metal. It’s that you’ll get addicted. I’d hate to count up how many hours I spent to set this up and learn how to use it. But once you get accustomed to having cast-to-order parts, it’s pretty hard to go back. So weigh carefully whether you need yet another excuse to never throw anything away!
Rob Rohde-Szudy
Madison, Wisconsin, USA
[email protected] |